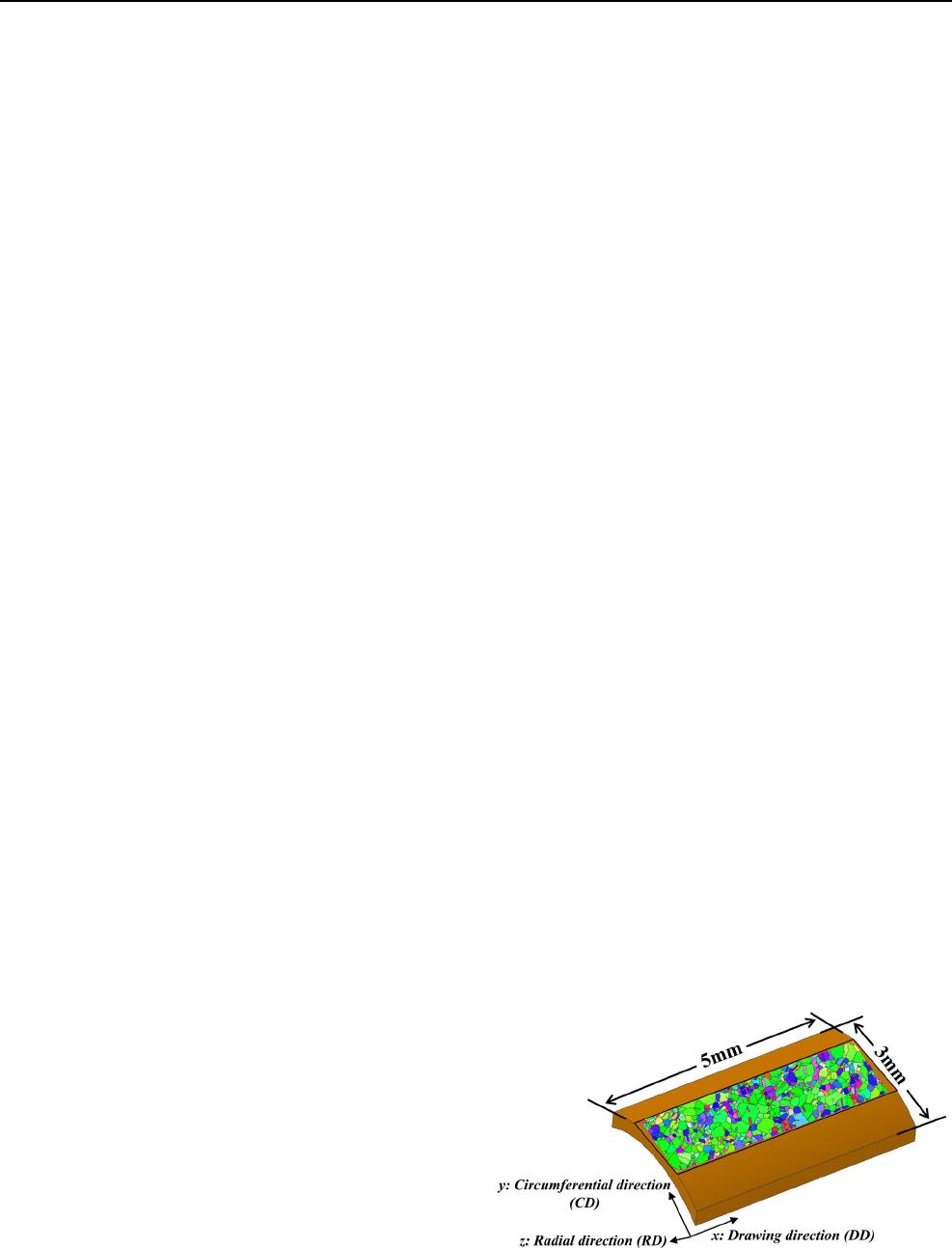
S.-W.Wang et al.
1 3
electron backscattered diffraction (EBSD) makes it possible
to investigate and understand the potential sources for the
behaviors found in earlier works. Nowadays, the microstruc-
tural behavior and annealing twin evolution in nickel [4,
22], nickel-based superalloy [23, 24], and super-austenitic
steel [25] were investigated by EBSD method. The former
researches also indicated that not only the materials but also
the predeformation process and initial deformation texture
are essential for the microstructural evolution during anneal-
ing process.
With an aim to understand the recrystallization behavior
during the heat treatment, the studies have been carried out
to figure out the evolution of texture and the microstructure
in pure copper. The effect of cold rolling process on texture
evolution of pure copper has been well investigated [26–29]
that shows the cube orientation as a recrystallization texture
and the formation mechanisms have been proposed as the
oriented growth theory. Anand etal. [30] characterized the
annealed pure copper sheet after cryo-rolling process and
found that with the increase of annealing time, the sample
shows a weakening of Brass texture, then exhibits almost
random texture, and finally forms the strong cube texture,
while the cold-rolled Al-0.3% Cu develops a strong Goss
texture during annealing treatment which is related to the
oriented nucleate mechanism [31]. Choi etal. [32] proposed
the strain energy release maximization model to predict the
texture changes of copper electrodeposits after recrystalliza-
tion. Also, the cold-drawn copper wires have been studied
by Baudin etal. [33] after recrystallization, and the results
showed the 〈100〉 fiber increases at the expense of the other
texture components. Nowfal etal. [34] used the synchrotron
diffraction method to investigate the local texture gradient
through the wall thickness of SF-Cu tubes with an average
wall thickness of 10mm. The structure consists of recrystal-
lized equiaxed grains with twins, and the dominant texture
component is the {001} 〈100〉 cube component.
To the knowledge of the authors, little efforts were taken
to study the annealing twins and recrystallization textures
of the thin-walled copper tubes. The precision copper tube
with a diameter of 6mm and a wall thickness of 0.3mm
was manufactured by the float-plug drawing process, which
exhibited a unique deformation microstructure and textures
[35, 36]. The copper tube was widely used in refrigeration
industries, due to its excellent thermal conductivity and plas-
ticity. Usually, a heat treatment process is necessary after
the deformation in order to release the stored energy of cold
work. Thus, the microstructural evolution during recrystal-
lization process is crucial for the final properties [37, 38],
such as fatigue resistance, corrosion resistance, and mechan-
ical properties. The purpose of this study is to investigate
the annealing twin boundaries as well as recrystallization
texture of the copper tube during the heat treatment. Firstly,
an evolving structure was obtained by taking the samples at
different heating stages. Then, the EBSD technology was
utilized to analyze the evolution of microstructure and the
textures during the recrystallization process.
2 Experimental
Highly purified oxygen-free copper tube billet (99.997%
pure) was deformed by float-plug drawing process to obtain
a Ф6 × 0.3mm final tube as an initial material. The initial
tube was cut into the segments about 200mm long, and
the segments were vacuum packaged with quartz tube to
prevent oxidation of surface. Then, the heat treatment was
carried out on the segments by using the electric resistance
furnace, from room temperature to 900 °C without holding
time. To examine the evolution of microstructure, the single
segment was taken out at 200 °C, 300 °C, 400 °C, 500 °C,
700 °C, and 900 °C, respectively, and then water-quenched
immediately to maintain the microstructure.
The annealing microstructures were analyzed by EBSD.
The samples with size of 5mm in length (drawing direction,
DD), 3mm in width (circumferential direction, CD), and
0.3mm in thickness (radial direction, RD) were cut from the
wall thickness of annealed tubes, seen as Fig.1. The local
coordinate system used to identify the direction of inverse
pole figure (IPF) and pole figure (PF) is also presented in
Fig.1. The x-, y-, and z-axis correspond to DD, CD, and RD
direction, respectively. The RD direction is the normal direc-
tion of the observation surface (DD-CD). The DD-CD sec-
tion was ground slightly to obtain a smooth plane and then
polished with diamond paste and finished with ion milling
to remove the surface deformation layer. EBSD examina-
tions were carried out using a FEI Nova Nano SEM 430
field-emission scanning electron microscope equipped with
a fully automatic HKL Technology EBSD attachment oper-
ated at 20kV. The HKL Channel 5 software was used for the
EBSD information collection and characterization. EBSD
maps were acquired using step sizes of 0.12–0.5µm to ana-
lyze the twins and substructures in the observation plane
Fig. 1 Observation surface of the samples for EBSD measurement