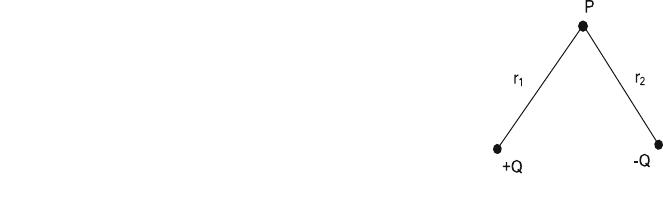
However, they did not connect the strength of the magnetic leakage field to the
strength of the magnetizing field and the permeability. They used two-dimensional
models. The main progress of the analytical met hod of magnetic leakage field analysis
was completed by Edwards and Palmer in 1986 [5]. They perfected the magnetic
dipole model. The shape parameters of the defect, the magnetizing field strength, the
permeability, and the magnetic flux leakage of the material were firstly connected.
The limitation of Edwards and Palmer’s model was that the permeability of the
material was supposed as a linear parameter in the derivation process. So there were
some errors between the theoretical results and the experimental results.
Therefore, numerical calculation method is usually adopted. The numerical cal-
culation method overcomes the limitation of the magnetic dipole model. In the
numerical calculation method of magnetic leakage field, the finite element method is
used most widely. Lord and Hwang first introduced the finite element method to the
calculation of the magnetic leakage field in 1975. They studied the effects of different
shapes, different dip angles, and the depth and width of crack on the magnetic
leakage field. It was pointed out that the numerical calculation was the only feasible
method for solving the problem of magnetic leakage field in the nonlinear and
complex shape defects [6]. The results of Lord and Hwang showed that the peak–
valley values of the magnetic leakage field were approximately linear proportional to
the increase of the depth of the defect. In 1986, the researches of Hwang and Lord
were tested by Foster, and the results of Lord and Hwang were modified [7]. In
1980s and 1990s, Atherton [8, 9] and Bruder [10] et al. did a lot of work in the
numerical calcul ation of the magnetic leakage field. Atherton calculated the defects
of the pipe wall and obtained a two-dimensional distrib ution model of the magnetic
leakage field. Altschuler Eduardo proposed the detection model of nonlinear crack
defect in steel pipe in 1995. He concluded that the induction intensity of the mag-
netic leakage was approximately linear with the increase of the crack depth [11].
In view of the characteristics of the inverse problem of magnetic flux leakage
detection, the existing methods can be classified as follows:
The direct metho d is to obtain the solution of the inverse problem by solving the
Green equation. However, it is difficult to solve the Green equation. Because of the
solving difficulty in direct method, the indirect method to solve the defect param-
eters is proposed. These methods can be divided into three categories: mapping
method, iterative method, and signal classification method (Fig. 6.2).
Fig. 6.1 Magnetic dipole
model
186 6 Magnetic Flux Leakage Testing