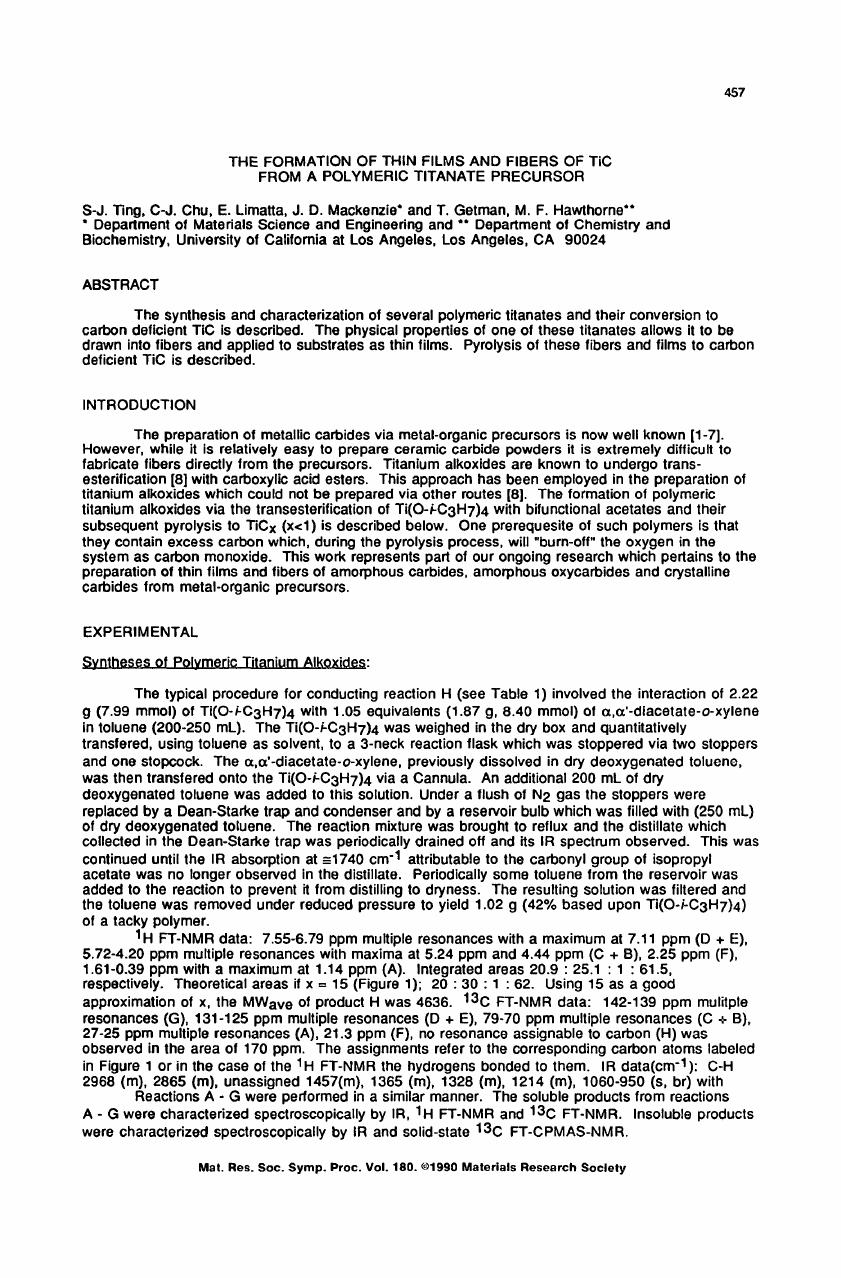
457
THE
FORMATION
OF
THIN
FILMS
AND
FIBERS OF
TiC
FROM
A
POLYMERIC
TITANATE
PRECURSOR
S-J.
Ting,
C-J.
Chu,
E.
Limatta,
J.
D.
Mackenzie*
and
T.
Getman,
M.
F.
Hawthorne-
Department
of
Materials
Science
and
Engineering
and
**
Department
of
Chemistry
and
Biochemistry,
University
of
California
at
Los
Angeles,
Los
Angeles,
CA
90024
ABSTRACT
The
synthesis
and
characterization
of
several
polymeric
titanates
and
their conversion
to
carbon
deficient
TIC
is
described.
The
physical
properties
of
one
of
these
titanates
allows
it
to
be
drawn
into
fibers
and
applied to
substrates
as
thin
films.
Pyrolysis
of
these
fibers
and
films
to
carbon
deficient
TiC
is
described.
INTRODUCTION
The
preparation
of
metallic
carbides
via
metal-organic
precursors
is
now
well
known
[1-7].
However,
while
it
is
relatively
easy
to
prepare
ceramic carbide
powders it
is
extremely
difficult
to
fabricate
fibers
directly from
the
precursors.
Titanium
alkoxides
are
known
to
undergo
trans-
esterification
[81
with
carboxylic
acid
esters.
This
approach
has
been
employed
in
the preparation
of
titanium
alkoxides
which
could
not
be
prepared
via
other
routes
[8].
The
formation
of
polymeric
titanium
alkoxides
via
the transesterification
of
Ti(O-iC3H7)4
with
bifunctional
acetates
and
their
subsequent
pyrolysis
to
TiCx
(x<l)
is
described
below.
One
prerequesite
of
such
polymers
is
that
they
contain
excess
carbon
which,
during
the
pyrolysis
process,
will
"burn-off"
the
oxygen
in
the
system
as
carbon
monoxide.
This
work
represents
part
of
our
ongoing
research
which
pertains
to the
preparation
of
thin
films
and
fibers
of
amorphous
carbides, amorphous
oxycarbides and
crystalline
carbides
from
metal-organic
precursors.
EXPERIMENTAL
Syntheses
of
Polymeric
Titanium
Alkoxides:
The
typical
procedure
for
conducting
reaction
H
(see
Table
1)
involved
the
interaction
of
2.22
g
(7.99
mmol)
of
Ti(O-i-C
3
H7)4
with
1.05
equivalents
(1.87
g,
8.40
mmol)
of
a,cz'-dlacetate-o-xylene
in
toluene
(200-250
mL).
The
Ti(O-i-C
3
H7)4
was
weighed
in
the
dry
box
and
quantitatively
transfered,
using
toluene
as
solvent,
to
a
3-neck
reaction flask
which
was
stoppered
via
two
stoppers
and
one stopcock.
The
c,c,-diacetate-o-xylene,
previously
dissolved
in
dry
deoxygenated
toluene,
was
then transfered
onto
the
Ti(O-i-C
3
H
7
)
4
via
a
Cannula.
An
additional
200
mL
of
dry
deoxygenated
toluene
was
added
to
this
solution. Under
a
flush
of
N2
gas
the stoppers
were
replaced
by
a
Dean-Starke
trap
and
condenser
and
by
a reservoir
bulb
which
was
filled
with
(250
mL)
of
dry
deoxygenated
toluene.
The
reaction
mixture
was
brought to
reflux
and
the
distillate
which
collected
in
the
Dean-Starke
trap was
periodically
drained
off
and
its
IR
spectrum
observed.
This
was
continued
until
the
IR
absorption
at
_-1740
cm-
1
attributable to
the
carbonyl
group
of
isopropyl
acetate
was
no
longer
observed
in
the
distillate.
Periodically
some
toluene
from
the
reservoir
was
added
to
the
reaction
to
prevent
it
from distilling
to
dryness.
The
resulting
solution
was
filtered
and
the
toluene
was
removed
under reduced
pressure
to
yield
1.02
g (42%
based
upon
Ti(O-i-C
3
H7)4)
of
a
tacky polymer.
1
H
FT-NMR
data:
7.55-6.79
ppm
multiple
resonances
with
a
maximum at
7.11
ppm
(D
+ E),
5.72-4.20
ppm
multiple
resonances
with
maxima
at
5.24
ppm
and
4.44
ppm
(C
+
B),
2.25
ppm
(F),
1.61-0.39
ppm
with
a
maximum
at
1.14
ppm
(A).
Integrated
areas
20.9
:
25.1
: 1
:
61.5,
respectively.
Theoretical
areas
if x
=
15 (Figure
1);
20
:
30
: 1 :
62.
Using
15
as a
good
approximation
of
x,
the
MWave
of
product
H
was
4636.
13
C
FT-NMR
data:
142-139
ppm
mulitple
resonances
(G),
131-125 ppm
multiple
resonances
(D +
E),
79-70 ppm
multiple
resonances
(C
+ B),
27-25 ppm
multiple
resonances
(A),
21.3 ppm
(F), no
resonance
assignable
to
carbon
(H) was
observed
in
the
area
of
170
ppm.
The
assignments
refer
to
the
corresponding
carbon
atoms
labeled
in
Figure
1 or
in
the
case
of
the
1
H
FT-NMR
the hydrogens
bonded
to
them.
IR
data(cm-1):
C-H
2968
(m),
2865
(m),
unassigned
1457(m), 1365
(m),
1328
(m),
1214
(m),
1060-950
(s,
br)
with
Reactions
A -
G
were
performed
in
a
similar
manner.
The soluble
products
from
reactions
A -
G
were
characterized
spectroscopically
by
IR,
1
H
FT-NMR
and
13
C FT-NMR.
Insoluble
products
were
characterized
spectroscopically
by
IR
and solid-state
13
C
FT-CPMAS-NMR.
Mat.
Res.
Soc.
Symp. Proc.
Vol.
180.
@1990
Materials
Research Society
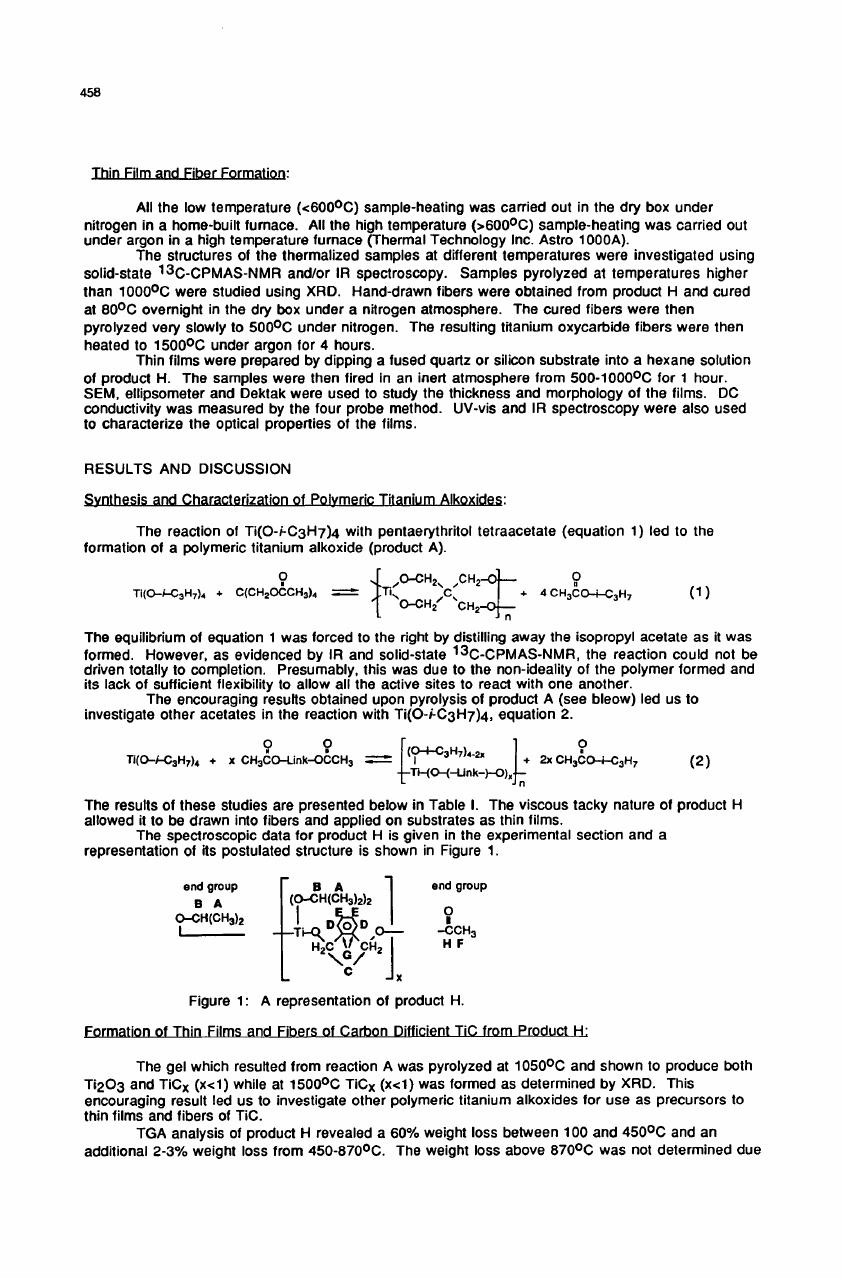
458
Thin
Film
and
Fiber
Formation:
All
the
low
temperature
(<600
0
C)
sample-heating
was
carried
out
in
the
dry box
under
nitrogen
in
a
home-built
furnace.
All
the
high
temperature
(>600
0
C)
sample-heating
was
carried
out
under
argon
in
a
high
temperature
furnace
(Thermal
Technology
Inc.
Astro
1
OOOA).
The
structures
of
the
thermalized
samples
at different
temperatures
were
investigated
using
solid-state
13
C-CPMAS-NMR
and/or
IR
spectroscopy.
Samples
pyrolyzed
at
temperatures
higher
than
1000
0
C
were
studied
using
XRD.
Hand-drawn fibers
were
obtained
from
product
H and
cured
at
80
0
C
overnight
in
the
dry box
under
a
nitrogen
atmosphere.
The
cured
fibers
were
then
pyrolyzed
very
slowly
to
500
0
C
under
nitrogen.
The resulting
titanium
oxycarbide fibers
were then
heated
to 1500
0
C
under
argon
for
4
hours.
Thin
films
were
prepared
by
dipping
a
fused
quartz
or
silicon
substrate
into
a
hexane
solution
of
product
H.
The
samples
were
then
fired
in
an
inert
atmosphere
from
500-1000
0
C
for
1
hour.
SEM,
ellipsometer
and
Dektak
were
used
to
study
the
thickness and
morphology
of
the
films.
DC
conductivity
was
measured
by
the
four
probe
method.
UV-vis
and IR
spectroscopy were
also
used
to
characterize
the
optical
properties
of
the
films.
RESULTS
AND
DISCUSSION
Synthesis
and
Characterization
of
Polymeric Titanium
Alkoxides:
The
reaction
of
Ti(O-i-C
3
H7)4
with
pentaerythritol
tetraacetate
(equation 1)
led
to
the
formation
of
a
polymeric
titanium alkoxide
(product
A).
0
-,,0OCH
2
,
,CH
2
-O--
0
Ti(O-.-C
3
HT)4
+
C(CH2OCCH
3
)
4
rTilO
CHc -
+
4 CH
3
CO--i-C
3
7
(1)
The
equilibrium
of
equation
1 was
forced
to
the
right
by
distilling
away
the
isopropyl
acetate
as
it
was
formed. However,
as
evidenced
by
IR and
solid-state
1
3
C-CPMAS-NMR,
the
reaction
could
not
be
driven
totally
to
completion.
Presumably,
this
was
due
to
the
non-ideality
of
the
polymer formed
and
its
lack
of
sufficient
flexibility
to allow
all
the
active
sites
to
react
with
one
another.
The
encouraging results
obtained
upon
pyrolysis
of
product
A
(see
bleow)
led
us
to
investigate
other
acetates
in
the
reaction
with
Ti(O-i-C
3
H7)
4
,
equation
2.
9
9 17
[-.-C
H~
"Ti(o-i-C
3
H
7
)
4
+ x
CH
3
CO-Unk-OCCH
3
-
I'-CH7)4.2x
2x
CH
3
CO-J-C
3
H
7
(2)
-L-T-{-Unk-)-O)-.•
The
results
of
these
studies are
presented
below
in
Table
I.
The
viscous
tacky
nature
of
product
H
allowed
it
to
be
drawn
into
fibers
and
applied
on
substrates
as
thin
films.
The
spectroscopic
data
for
product
H
is
given
in
the
experimental
section
and
a
representation
of
its
postulated
structure
is
shown
in
Figure
1.
end
group
B
A
end
group
B
A
(O-CH(CH
3
)
2
)
2
.O-H(CH
3
)
2
D•I
I
L..-
T`.-Q,
0
D 0-
-CCH
3
L
c
.j
Figure
1:
A representation
of
product
H.
Formation
of
Thin
Films
and
Fibers
of
Carbon
Difficient
TiC
from
Product
H:
The
gel
which
resulted
from
reaction
A was
pyrolyzed
at
1050
0
C
and
shown
to
produce
both
Ti203
and
TiCx
(x<l)
while
at
1500
0
C TiCx
(x<l)
was
formed
as
determined
by
XRD. This
encouraging
result
led
us
to
investigate
other
polymeric
titanium
alkoxides
for
use
as
precursors
to
thin
films
and
fibers
of
TiC.
TGA
analysis
of
product
H
revealed
a
60%
weight
loss
between
100
and
450
0
C
and
an
additional
2-3%
weight
loss
from
450-870
0
C.
The
weight
loss above
870
0
C
was
not
determined
due
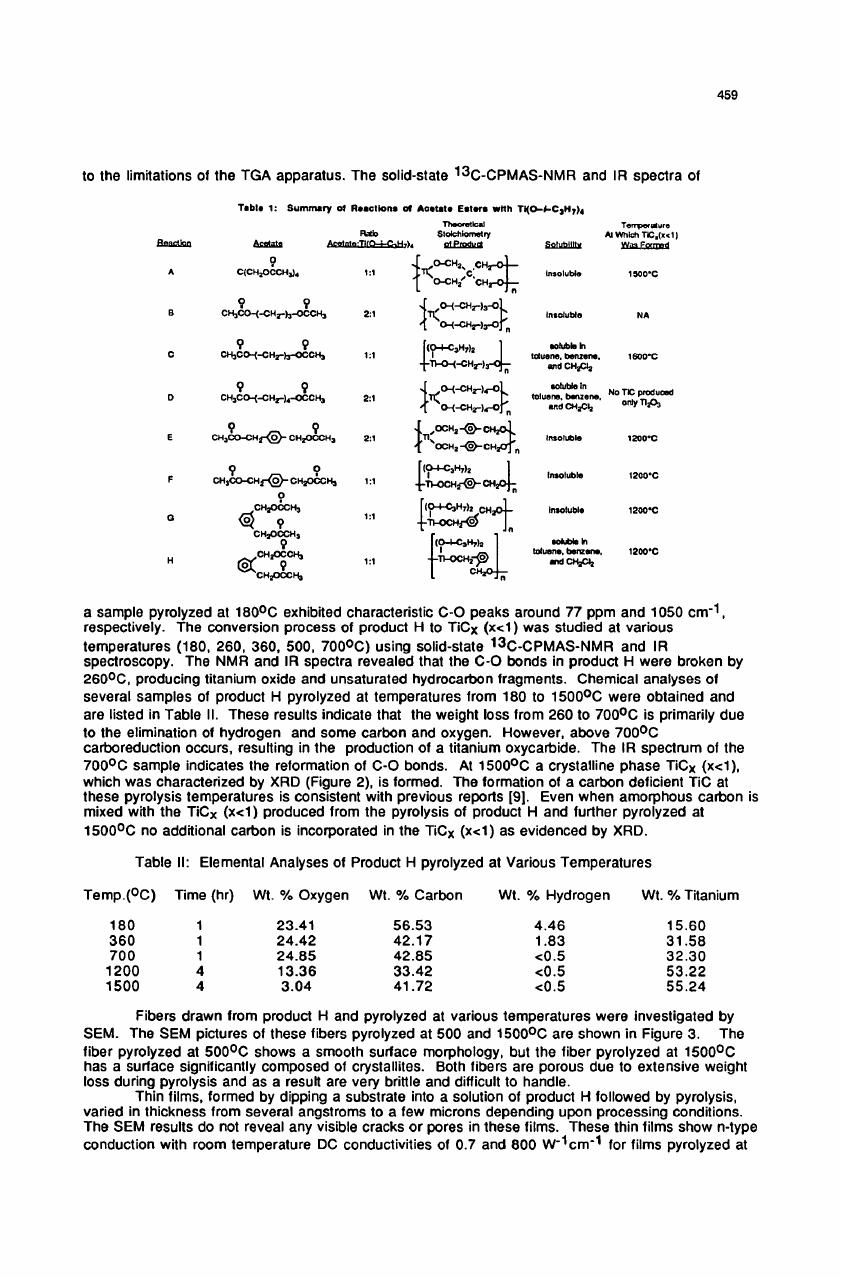
459
to
the
limitations
of
the
TGA
apparatus.
The
solid-state
13
C-CPMAS-NMR
and
IR
spectra
of
Table 1:
Summary
at
Reactions
of
Acetate
Eaters
with
Ti(O.-.-C3H,)
Bsa1ns
Thesetca
RAID
Stlotlchoetry
Acetato
A~sdXLQ=rkM)4
o cLmraug
0
A C(CHOCCH
3
)
4
9
9
CH
3
CO-(-CH7-)
3
-OCCH
3
9
9
C CHnCO-(-CH-.-OhCCHn
9
9
0 CH
3
CO-(-CH2-)
4
-OCCN
3
9
9
E
CH300-CHjr- CH
2
00CH
3
9
9
F CH
3
CO-CHfr"-
CH
2
OCCH3
CH
2
00CH
3
CH
2
0CCH
3
9
HCH
2
OCCI
3
,.,O-CH2,
,H -
:1
<
'C:C•
-• _CH
2
.
.CH-O-.On
Terrp(sl)re
Al WhichTI1C.(W~)
Insoluble
Insoluble
1.1
-[-Hn-o+cHC)4
-;.
u•I.b
"
0-t
CH2-)
4
-0f
2:1
,,l•o-(-c~z-),-o•
4
cTu.,O-"
• CH
2
O
2:1
{
0ocH.-@-CH.,o",
1:1
(04-C
[to-ic,,.i,,tu
l
1:12
C
I 500C
NA
16DO'C
toluene,
benzene.
No
TC
producd
and
cHaC'2
only
To
3
lnsoolble
1200"C
Insoluble 1200°C
Insoluble
soluble n
toluana,
ltervans
and C14Cl,
1200*C
1200"C
a
sample
pyrolyzed
at
180
0
C
exhibited
characteristic
C-O
peaks
around
77
ppm
and
1050
cm-
1
,
respectively.
The
conversion
process
of
product
H
to
TiCx
(x<l)
was studied
at
various
temperatures
(180,
260,
360,
500,
700
0
C)
using
solid-state
13
C-CPMAS-NMR
and
IR
spectroscopy.
The
NMR
and IR
spectra
revealed
that
the
C-O
bonds in
product
H
were
broken
by
260
0
C,
producing
titanium
oxide
and
unsaturated
hydrocarbon
fragments.
Chemical
analyses
of
several
samples
of
product
H
pyrolyzed
at
temperatures
from
180
to
1500
0
C
were
obtained and
are
listed
in
Table
II.
These
results
indicate
that
the
weight
loss
from
260
to
700
0
C is
primarily
due
to
the
elimination
of
hydrogen
and
some
carbon
and
oxygen.
However,
above
700
0
C
carboreduction
occurs,
resulting
in
the
production
of
a
titanium
oxycarbide.
The
IR spectrum
of
the
700
0
C
sample
indicates
the
reformation
of
C-O
bonds.
At
1500
0
C
a
crystalline
phase
TiCx
(x<l),
which
was
characterized
by XRD
(Figure
2), is
formed.
The
formation
of
a
carbon
deficient
TiC
at
these
pyrolysis
temperatures
is
consistent
with
previous
reports
[9].
Even
when
amorphous
carbon
is
mixed
with
the
TiCx
(x<l)
produced
from
the
pyrolysis
of
product
H
and
further
pyrolyzed
at
1500
0
C
no
additional
carbon
is
incorporated
in
the
TiCx
(x<l)
as
evidenced
by
XRD.
Table
Ih:
Elemental
Analyses
of
Product
H
pyrolyzed
at
Various
Temperatures
Temp.(OC)
Time
(hr)
Wt.
%
Oxygen
Wt.
%
Carbon
Wt.
%
Hydrogen
Wt.
%
Titanium
180
360
700
1200
1500
4
4
23.41
24.42
24.85
13.36
3.04
56.53
42.17
42.85
33.42
41.72
4.46
1.83
<0.5
<0.5
<0.5
15.60
31.58
32.30
53.22
55.24
Fibers drawn
from
product
H
and
pyrolyzed
at various
temperatures
were
investigated
by
SEM.
The
SEM
pictures
of
these
fibers
pyrolyzed
at 500
and
1500
0
C
are
shown
in
Figure
3.
The
fiber
pyrolyzed
at
500
0
C
shows
a
smooth
surface
morphology,
but
the
fiber
pyrolyzed
at
1500
0
C
has
a
surface
significantly
composed
of
crystallites.
Both
fibers
are
porous
due
to
extensive
weight
loss
during
pyrolysis
and
as
a
result
are
very
brittle
and
difficult
to
handle.
Thin
films,
formed
by
dipping
a
substrate
into
a
solution
of
product
H
followed
by
pyrolysis,
varied
in
thickness
from
several angstroms
to
a
few
microns
depending
upon
processing
conditions.
The
SEM
results
do
not
reveal
any
visible
cracks
or pores
in
these
films.
These
thin
films
show
n-type
conduction
with
room
temperature
DC
conductivities
of
0.7
and
800
W'
1
cm"
1
for
films
pyrolyzed
at
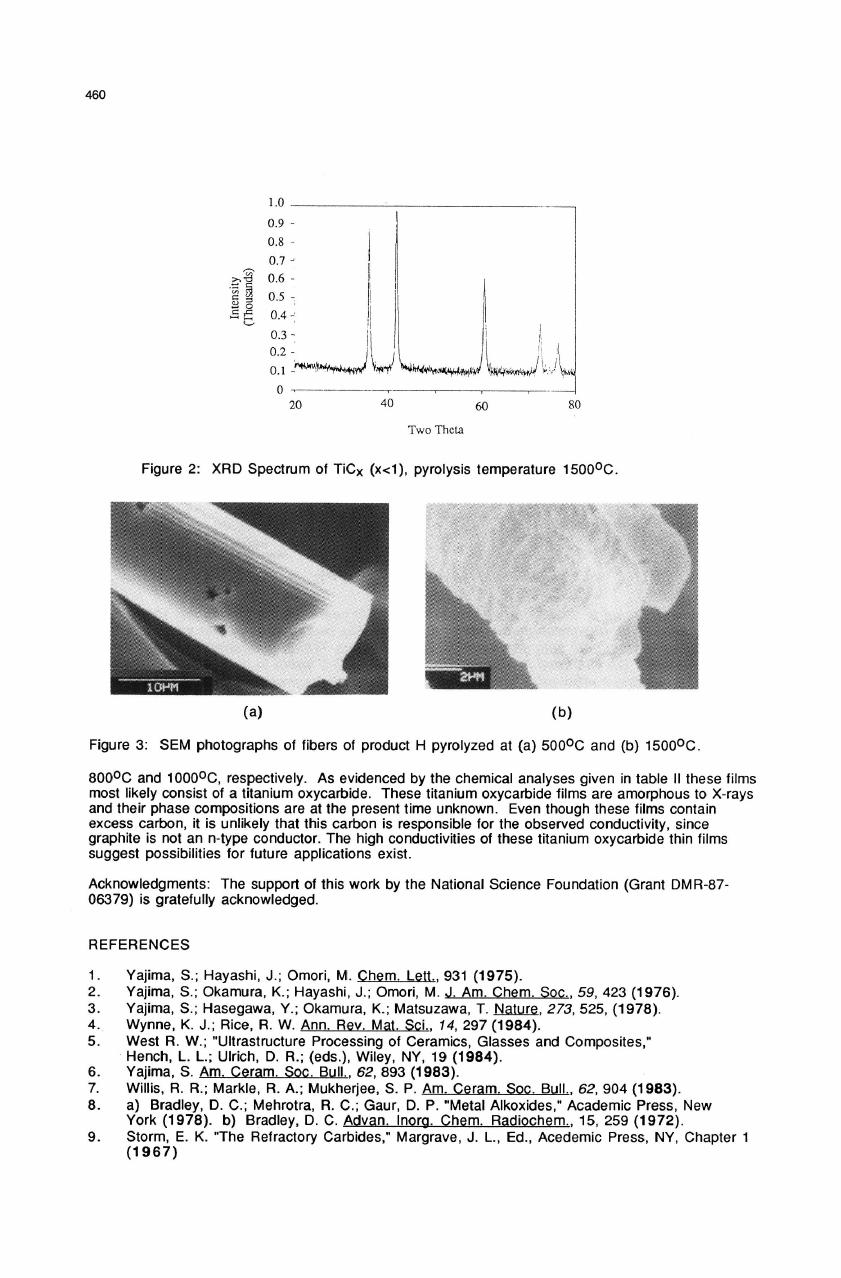
460
1.0
0.9
0.8
0.7
0.6
0.5
-
0.4
-
0.3-
0.
1
0-.---1
_
20
40
l4
h
60
80
Two
Theta
Figure
2:
XRD
Spectrum
of TiCx
(x<l),
pyrolysis
temperature
1500
0
C.
(a)
(b)
Figure
3: SEM
photographs
of
fibers
of
product
H
pyrolyzed
at (a)
5000C
and
(b)
15000C.
800
0
C
and
1000
0
C,
respectively.
As
evidenced
by
the
chemical
analyses
given
in
table
II
these
films
most
likely
consist
of
a
titanium
oxycarbide.
These
titanium
oxycarbide
films
are
amorphous
to
X-rays
and
their
phase
compositions
are
at
the
present
time unknown.
Even
though
these
films
contain
excess
carbon,
it
is
unlikely
that
this
carbon
is
responsible
for
the
observed
conductivity,
since
graphite
is
not
an
n-type
conductor.
The
high
conductivities
of
these
titanium
oxycarbide
thin
films
suggest
possibilities
for
future
applications
exist.
Acknowledgments:
The
support
of
this
work
by
the
National
Science
Foundation (Grant
DMR-87-
06379)
is
gratefully
acknowledged.
REFERENCES
1.
Yajima,
S.;
Hayashi,
J.;
Omori,
M.
Chem.
Lett.,
931
(1975).
2.
Yajima,
S.;
Okamura,
K.;
Hayashi, J.;
Omori,
M.
J.
Am.
Chem.
Soc.,
59,
423
(1976).
3.
Yajima,
S.;
Hasegawa,
Y.;
Okamura,
K.;
Matsuzawa,
T.
Nature,
273,
525,
(1978).
4.
Wynne,
K.
J.;
Rice,
R.
W.
Ann.
Rev.
Mat.
Sdi., 14,
297
(1984).
5.
West
R.
W.;
"Ultrastructure
Processing
of
Ceramics,
Glasses
and
Composites,"
Hench,
L.
L.;
Ulrich,
D.
R.;
(eds.),
Wiley,
NY,
19
(1984).
6.
Yajima,
S.
Am.
Ceram.
Soc.
Bull.,
62,
893
(1983).
7.
Willis,
R.
R.;
Markle,
R.
A.;
Mukherjee,
S.
P.
Am.
Ceram. Soc.
Bull.,
62,
904
(1983).
8.
a) Bradley,
D.
C.;
Mehrotra,
R.
C.;
Gaur,
D.
P.
"Metal
Alkoxides,"
Academic
Press,
New
York
(1978).
b)
Bradley,
D.
C.
Advan.
Inorg.
Chem.
Radiochem.,
15,
259
(1972).
9.
Storm,
E. K.
"The
Refractory
Carbides,"
Margrave,
J.
L.,
Ed.,
Acedemic
Press,
NY,
Chapter
1
(1967)